How Recycled American Batteries Pollute Communities Around the World
From James Morton Turner's Cundill Prize-Nominated Charged
In the early 1990s, Peru undertook a privatization program as part of a broader turn toward neoliberalism, undoing the socialist legacy of its 1970s military government, that included selling off state-owned oil, energy, telecommunications, and mining companies. Just before Peru auctioned off the La Oroya smelter complex, the US-based magazine Newsweek warned, “If anyone’s interested, hell is up for sale.” The eventual buyer was Doe Run Peru, which was owned and run by the same New York-based company that owned the Herculaneum smelter in Missouri. It purchased the smelter for $247 million and committed to a $120 million program plan to modernize the plant and reduce pollution.
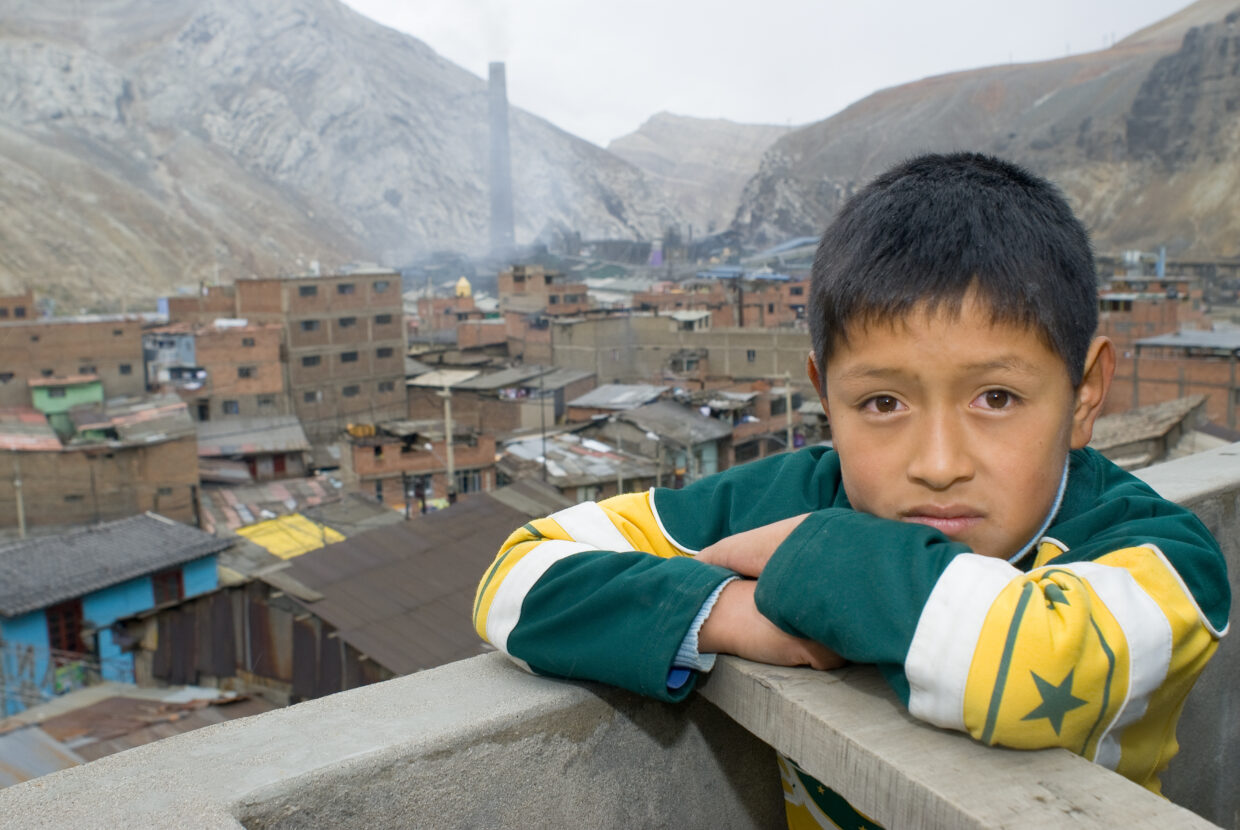
Although Doe Run Peru would be vilified for its efforts, the company made substantial investments in La Oroya in the early 2000s, including plant upgrades, worker hygiene programs, and a community outreach initiative. It launched programs to lower blood lead levels by promoting what it described as “a culture of hygiene and health intended to decrease blood lead levels” especially among children. Ambient airborne lead pollution fell by more than 50 percent, and, according to Doe Run’s analyses, average blood lead levels in children dropped to 26.1 µg/dL. Despite Doe Run Peru’s improvements, however, it did not undertake the more expensive retrofits that promised the greatest reductions in pollution.
The global consequences of recycling lead-acid batteries are astounding.Public pressure mounted for action to clean up La Oroya. In 2006, the Blacksmith Institute placed La Oroya on its inaugural list of the ten most-polluted places in the world. And in the winter of 2006, Mother Jones ran a feature on Doe Run, drawing parallels between the company’s operations in Missouri and those in Peru. This surge of international attention to conditions in La Oroya stemmed from the work of US-based Protestant missionaries, who responded to a plea for help from local evangelicals in La Oroya in 2002. Their partnership led to what one US-based missionary described as a “transnational campaign for children’s health in La Oroya.”
Doe Run never followed through fully on its commitment to upgrade operations in La Oroya. In the wake of the 2008 financial crisis, Doe Run Peru filed for bankruptcy. Peru reclaimed the smelter as Doe Run Peru’s largest creditor. By the end of 2017, 1,600 citizens of La Oroya, primarily children, were party to lawsuits filed in state and federal courts in Missouri alleging damages from Doe Run’s Peruvian operations. Despite Doe Run’s extensive efforts to dodge liability for pollution in La Oroya, those suits continued to proceed through US courts in 2020. In turn, Doe Run sought legal redress for what it deemed to be Peru’s illegal seizure of its operations.
The crisis in La Oroya reflected a broader trend in the lead industry. Less US primary lead production meant more imported lead from countries like Peru, South Korea, and China, all of which had weaker standards for protecting workers and public health. Between 2000 and 2010, lead smelting in China quadrupled from one to four million tons per year, with primary lead smelting accounting for nearly two-thirds of production. During that time, China became the largest destination of lead ore concentrates exported from the United States. Local protests in China, scholarly research, and international media coverage drew attention to problems with lead pollution in China too.
Closing secondary lead smelters in the United States in the early 2000s also pushed more lead-acid battery recycling abroad. This had first been a concern in the 1980s, when the US lead recycling industry nearly collapsed. Scrap batteries from the United States began turning up in countries such as India, Mexico, South Korea, Venezuela, and Taiwan. In 1990, PBS’s Frontline aired an episode titled “The Global Dumping Ground” that focused on the international trade in hazardous waste. It spotlighted the ill consequences of recycling US batteries in Taiwan. Although restrictions were adopted on international trade in hazardous waste in the 1990s, including the Basel Convention on the Control of Transboundary Movements of Hazardous Wastes and Their Disposal, those regulations initially included a loophole for materials destined for recycling, such as lead-acid batteries.
____________________________________
Charged: A History of Batteries and Lessons for a Clean Energy Future by James Morton Turner has been shortlisted for the 2023 Cundill History Prize.
____________________________________
The largest foreign destination for spent US batteries has been Mexico. Exports surged from 4,300 metric tons of lead in 2000 to 200,000 metric tons of lead in 2010. Secondary smelter shutdowns in places like Pennsylvania, Texas, and the Exide smelter in California likely contributed to the growing transboundary trade. Johnson Controls’ acquisition of two Mexican smelters in the early twenty-first century, contributed to the surge of battery exports. Johnson Controls, the largest domestic lead-acid battery manufacturer at the time, described their acquisitions as part of a strategy to shore up their access to recycled lead. Many observers, however, including those in the lead industry, environmental health advocates, and economists, viewed the shift to Mexico as a race to the bottom driven by trade liberalization.
Under the terms of the North American Free Trade Agreement, member nations were encouraged to meet the same science-based occupational health and environmental standards. But that requirement was unevenly enforced. Mexican standards for lead were lower and less thorough than those in the United States: occupational exposure limits were three times the US standard (150 µg/m3 ); ambient pollution levels were 1.5 µg/m3 (the same as the US standard prior to 2008); and worker blood lead levels were unregulated. The New York Times reported in 2011 that the “rising flow of batteries is a result of strict new Environmental Protection Agency standards on lead pollution,” which made it more expensive to recycle in the United States while doing nothing to prevent “exporting the work and the danger to countries where standards are low and enforcement is lax.”
Public health activists led by US-based OK International and Mexico-based Fronteras Comunes succeeded in drawing substantial attention to the issue of lead-acid battery exports in the early 2000s. Their goal was a ban on exports. The NAFTA-created Commission for Environmental Cooperation undertook an in-depth investigation, faulting the weak regulatory standards in Mexico. US-based secondary lead smelters voiced objections to the exports: “Every day that scrap batteries are exported from the U.S. to Mexico and other nations is another day that the U.S. poisons our neighbors’ children.” Public health economists documented a relationship between the increase in lead exports to Mexico and poor health outcomes for Mexican children living in proximity to the smelters. Yet, the public pressure succeeded only in improving regulations for documenting the trade in spent lead-acid batteries, not imposing limits on such exports.
Lead’s toll is measured in diminished mental capacity and chronic health ailments that last a lifetime.The most troubling fate of lead-acid batteries is the one that is hardest to follow: the flow of batteries to countries least well-equipped to recycle them safely. Compared to the volume of batteries recycled domestically or the volume of batteries exported to Mexico, the percentage of US batteries that go to recycling operations in other countries is relatively small. Yet, around the world, informal recycling operations, where lead batteries are smelted in open barrels or rudimentary furnaces, remain common. The small scale of such operations, their wide distribution, and the rapidity with which they are erected and dismantled means there is no comprehensive information about the informal lead-processing industry.
Such sites often draw attention only in moments of crisis. For instance, in the 1990s, a lead smelter near the port of Haina in the Dominican Republic resulted in an epidemic of local lead poisoning, with more than 90 percent of nearby residents testing above accepted levels. The site was described as the Dominican Chernobyl. In 2007, World Health Organization authorities became aware of an epidemic of lead poisoning outside Dakar, Senegal. Locals had been collecting lead fragments leftover in the sandy soil from battery recycling operations. Children often played in the sand. Sometimes adults brought soil to their homes to sieve and bag. Such activities resulted in lead exposure connected to the deaths of eighteen children in 2007 and 2008. In 2015, Phyllis Omido, a Kenyan, was awarded the Goldman Prize for environmental activism in recognition of her efforts to close a secondary lead smelter that operated with few precautions and sickened her son and her community. She was jailed for her efforts and violently attacked by two armed men. Ultimately, she was successful, forcing the closure of the smelter in March 2014.
When the consequences of such small-scale and unregulated lead recycling operations are factored in, the global consequences of recycling lead-acid batteries are astounding. Jack Caravanos, a professor of public health and lead researcher at the Blacksmith Institute, warned that “lead poisoning from improper automotive battery recycling activities is the number one childhood environmental health threat globally.” In few cases does the exposure result in death. Instead, lead’s toll is measured in diminished mental capacity and chronic health ailments that last a lifetime. It is estimated that one in three children worldwide suffer from elevated blood lead levels. Researchers surveying the literature on exposure from sites of lead pollution identified metal foundries and battery recycling as “more than likely some of the major contributors to hotspot lead poisoning worldwide.” And as the use of lead-acid batteries in many countries continues to grow, to service electric bikes, for small-scale power backup for solar arrays, and for automobiles, the challenges of safely managing lead-acid batteries at end of life are likely only to grow.
__________________________________
From Charged: A History of Batteries and Lessons for a Clean Energy Future by James Morton Turner. Copyright © 2023. Available from University of Washington Press.